What is the working principle of crystallizer?
- alaqua inc
- Mar 15
- 5 min read
A crystallizer, indeed, is a pivotal piece of equipment in numerous industrial processes, transforming liquid solutions into solid crystals. From the table salt we sprinkle on our food to the life-saving pharmaceuticals we rely on, the outputs of crystallizers permeate our daily lives. The crystallizer working principle underpins these diverse applications, making it essential to understand its mechanics.
Let's delve into its detailed workings, exploring the science that turns liquids into precisely structured solids.
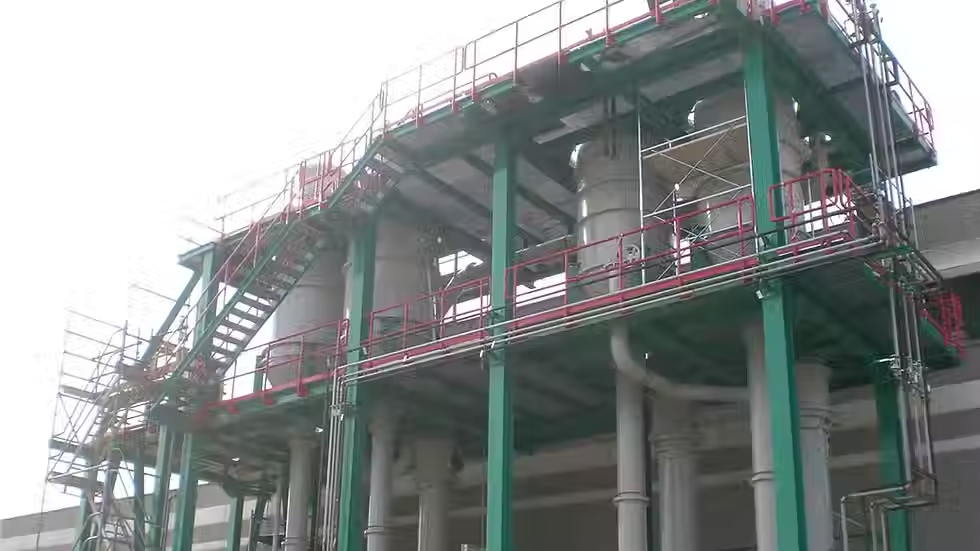
The Main Idea: What a Crystallizer Does
A crystallizer, essentially, establishes a supersaturated liquid environment. This means the liquid holds more dissolved substances than it normally can at equilibrium, thereby, creating an unstable state that drives crystal formation. Solid crystals, consequently, form from this excess, as the solute seeks to return to a stable solid phase. The crystallizer, moreover, strictly governs this formation process to ensure desired crystal properties, controlling factors like size, shape, and purity.
First, the system generates a supersaturated solution:
The process, notably, begins by carefully adding solute until the solution exceeds its normal holding capacity. This crucial step, specifically, creates an unstable environment where the solute is eager to leave the liquid phase.
This initial stage, furthermore, sets the foundation for crystal formation, as the excess solute seeks to return to a stable solid state.
Then, tiny crystal nuclei appear within the liquid:
These nuclei, in fact, act as starting points for crystal growth. They are, in other words, the seeds upon which the rest of the crystal structure will form.
Nucleation, often, can occur spontaneously, due to random fluctuations in the solution, or it can be induced by seeding, where small crystals are intentionally added to the solution.
Next, dissolved material adheres to these nuclei, causing growth:
Solute molecules, subsequently, migrate from the supersaturated solution to the surface of the existing crystal nuclei.
This deposition process, additionally, gradually increases the size of the crystals, layer by layer, until they reach the desired dimensions.
Finally, the process yields larger, defined crystals:
The crystals, ultimately, develop a specific shape and size, which are determined by the crystallizer's operating parameters and the properties of the solute.
The crystallizer, importantly, controls the final product's characteristics, such as crystal size distribution and purity, which are essential for downstream processing.
Understanding Nucleation in a Crystallizer
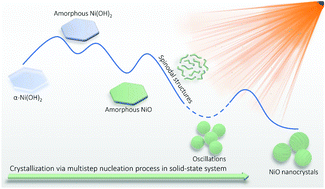
Nucleation, indeed, is the beginning of crystal formation. It's when the first tiny crystals start to appear.
Primary nucleation, naturally, happens spontaneously.
Secondary nucleation, conversely, occurs with existing crystals.
Controlling nucleation, therefore, is critical for crystal size.
Crystal Growth Mechanisms within a Crystallizer
Crystal growth, in essence, is the process of adding more molecules to the crystal.
Diffusion, primarily, brings solute molecules to the crystal surface.
Integration, then, incorporates these molecules into the crystal lattice.
The growth rate, naturally, depends on supersaturation and temperature.
Controlling Crystal Size Distribution in a Crystallizer
Crystal size distribution, notably, is the range of crystal sizes. It is, moreover, essential for product quality.
Maintain consistent supersaturation.
Control, carefully, nucleation and growth rates.
Use seeding, accordingly, to get a narrow distribution.
Getting the Liquid Just Right in the Crystallizer
Supersaturation, undeniably, is paramount. It is, indeed, the core of the crystallizer working principle. Several methods, for instance, achieve this critical step, each with its own advantages and applications.
Cool the liquid to reduce its solubility:
Lowering the temperature, specifically, decreases the liquid's ability to hold solute, forcing the excess solute to precipitate out as crystals. This method, generally, is commonly used for substances with a strong temperature dependence on solubility.
Remove some liquid through evaporation:
Evaporation, thus, concentrates the remaining solution by removing the solvent, increasing the solute concentration and leading to supersaturation. This method, furthermore, is effective for substances with a relatively high solubility.
Introduce a precipitating agent:
Adding a chemical that reacts with the solute, consequently, causes it to solidify, inducing rapid crystallization. This method, particularly, is useful when temperature or evaporation is not practical.
The crystallizer, naturally, must maintain precise control over these factors to achieve the desired crystal properties, ensuring consistent and high-quality output.
The Impact of Impurities on Crystallizer Function
Impurities, inevitably, can affect crystal growth. They can, moreover, change the crystal's shape, size, and purity.
Impurities, often, can block crystal growth.
They can, similarly, also change the rate of growth.
Purification steps, therefore, are often needed.
Monitoring and Control Systems in a Crystallizer
Modern crystallizers, notably, use advanced systems. They, in fact, monitor and control the process.
Sensors, primarily, measure temperature, concentration, and flow.
Control systems, then, adjust operating parameters.
Automation, consequently, improves consistency and efficiency.
How Heat and Mixing Help in the Crystallizer
Heat and mixing, undeniably, are crucial for crystal formation. They, moreover, directly influence the crystallization process, affecting both nucleation and growth rates.
Heat adjustments alter the liquid's capacity to hold dissolved substances:
Temperature variations, naturally, affect solubility and crystallization rates, requiring careful temperature control for uniform crystal growth. Precise temperature control, furthermore, prevents unwanted crystal growth and ensures a uniform crystal size distribution.
Consistent mixing ensures uniform distribution of solute and temperature:
Mixing, importantly, prevents localized supersaturation and temperature gradients, promoting even crystal growth throughout the crystallizer. Effective mixing, additionally, also helps to prevent the formation of large, undesirable crystals.
The crystallizer, consequently, regulates heat and mixing for optimal crystal output, ensuring efficient and predictable crystallization.
Types of Crystallizers and Their Applications

Different crystallizers, generally, fit different needs. They have, in fact, different designs.
Forced circulation crystallizers, primarily, are used for high-volume production.
Draft tube baffles crystallizers, then, are used for large crystals.
Fluidized bed crystallizers, similarly, are used for uniform crystal size.
Scale-Up Considerations for Crystallizer Design
Moving from lab to factory, undeniably, requires careful planning. Scale-up, indeed, is complex.
Maintain, consistently, similar supersaturation and mixing.
Account, carefully, for changes in heat transfer.
Ensure, naturally, consistent crystal quality.
Finding a Good Crystallizers Supplier
Selecting a reliable crystallizers supplier, notably, is vital for successful operation. Especially a crystallizer supplier in USA. They offer expert guidance and support, ensuring the equipment runs efficiently and reliably, and can also help with the optimization of the crystallizing process.
In conclusion
The crystallizer, undeniably, stands as a cornerstone of modern industrial processes, enabling the production of countless crystalline products. Understanding the intricate crystallizer working principle, ultimately, is not merely an academic exercise; it's a practical necessity for industries that rely on precise crystal formation. By carefully managing supersaturation, nucleation, and crystal growth, manufacturers, therefore, can achieve consistent and high-quality results. Furthermore, the selection of a reputable crystallizers supplier ensures that these processes are optimized for efficiency and reliability, contributing to the overall success of the operation. As technology advances, the design and operation of crystallizers will continue to evolve, further enhancing their capabilities and expanding their applications. Therefore, a firm grasp of these core principles remains essential for anyone involved in industries that utilize crystallization.
Looking for a trusted crystallizer supplier? Alaqua Machinery provides top-quality crystallizers designed for optimal performance and efficiency. With years of experience and a commitment to customer satisfaction, Alaqua Machinery delivers reliable solutions tailored to your specific needs. Contact Alaqua Machinery today to learn more about our crystallizer offerings and how we can help you achieve your production goals.
Comments